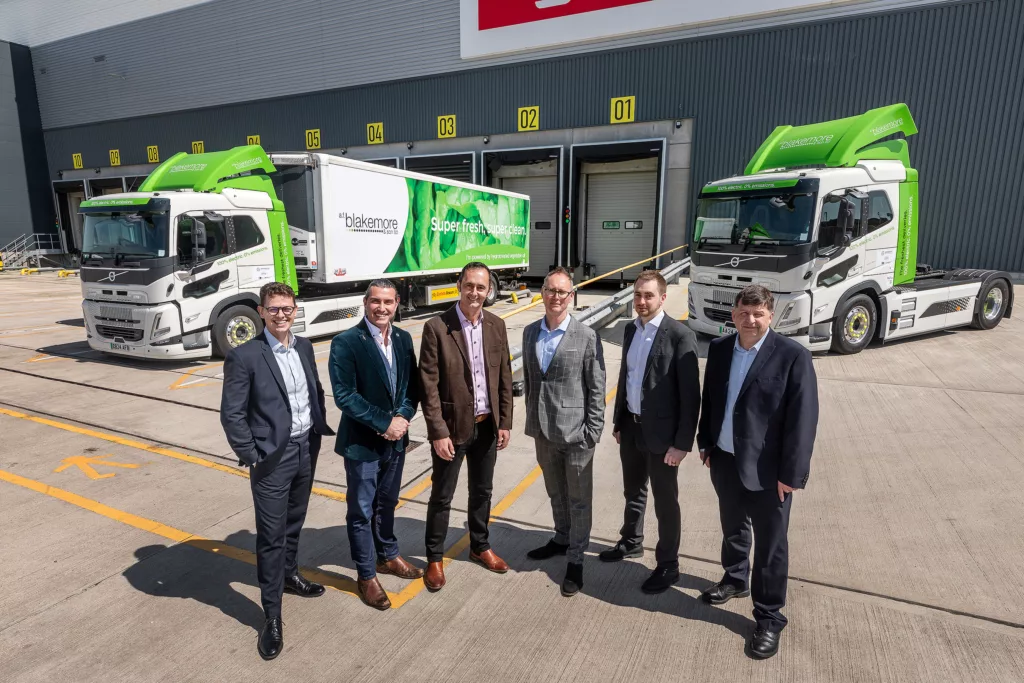
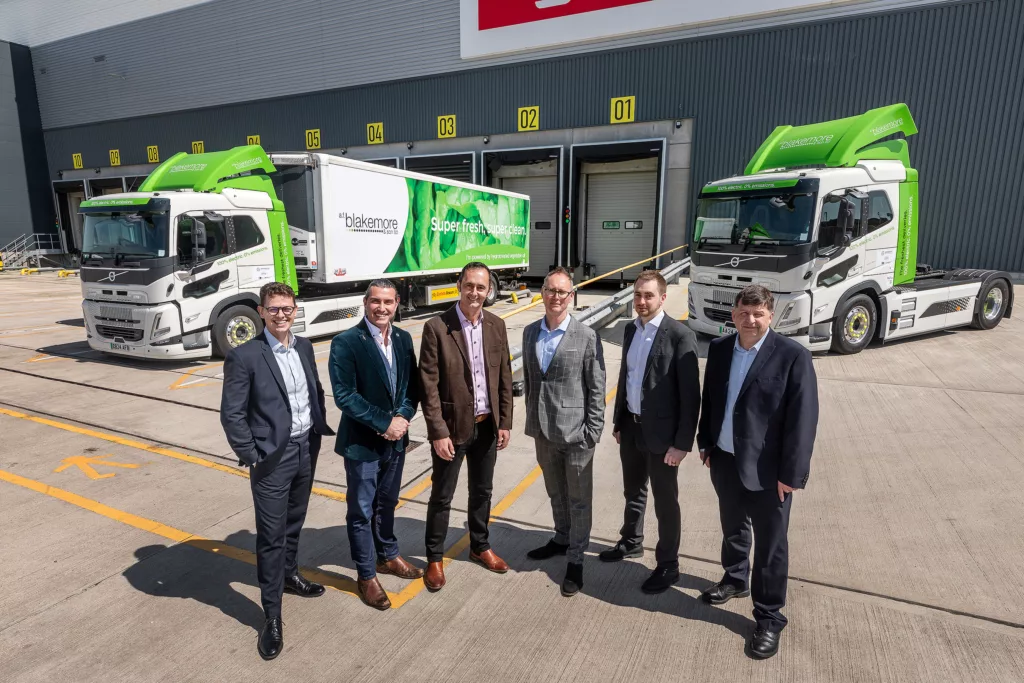
Electrification is a massive unknown for hauliers, which is why making that first step shows both determination and a genuine desire to help tackle the climate emergency.
So take a bow, A.F. Blakemore & Son. The family-owned retail and wholesale business, that is also the largest SPAR wholesaler in the UK and a consortium member of the GRIDSERVE Electric Freightway, has just taken delivery of the programme’s first fully electric Heavy Goods Vehicles (eHGVs).
Two Volvo FM Electric tractor units, coupled to refrigerated trailers powered by sustainable Hydrogenated Vegetable Oil (HVO), are now operating from the company’s 175,000 sq ft Bedford Depot, directly replacing roles that were previously performed by diesel-powered trucks.
A.F. Blakemore & Son estimates their inclusion in the fleet will save 45,000 litres of diesel and prevent more than 120 tonnes of carbon dioxide being emitted into the atmosphere each year.
That’s just from two electric trucks. Now imagine what could be achieved if the company could decarbonise its entire fleet of 103 articulated units, 178 trailers and 130 rigid HGV vehicles.
Bedford depot brilliance
The vast Bedford facility you’re looking at is one of several depots owned by A.F. Blakemore & Son. Built in 2020, it is the first depot to feature separate frozen, chilled and ambient temperature chambers in one location. Each warehouse chamber is roughly the same height as a five-storey building, with steel racking stretching skywards to house 4,500 different items of produce from cheese to crisps. It is a hive of beeping horns and hyperactivity, with pickers operating 24 hours a day and drivers delivering more than 7,000 cages of orders across 200 routes every week in the south and southeast of England.
Both electric trucks are being drafted straight into delivery duties, with their 540kWh batteries providing a maximum 185-mile range. The depot already has AC charging in place, but GRIDSERVE is working with A.F. Blakemore & Son to install High Power DC charging that would compress the charging time from several hours to less than two, meaning the eHGVs could be used to double shift, further improving each vehicle’s unit economics.
Trial and error
Sometimes, new stuff costs more money and it’s harder to pay for things you know you can get cheaper elsewhere (how that Nobel Prize for Economics alludes me, I’ll never know…). That’s the current challenge with electric trucks: we know everybody benefits from their silent propulsion and zero tailpipe emissions, but the list price is anywhere between two- and three times more expensive than a diesel-powered equivalent.
The purpose of the Electric Freightway programme, funded by the Department for Transport and delivered in partnership with Innovate UK, is to help level that playing field with both support and subsidy, to see how feasibly and quickly hauliers could decarbonise their fleets given the right conditions.
“It’s fantastic to be part of the Electric Freightway programme, but now we have the electric trucks on our fleet, it’s about learning as much as possible from them,” explains Dave Higgs, Group Compliance Officer at A.F. Blakemore & Son. “Initially, we worked with Volvo and our planning team to develop real-world range simulations for our routes, and we’re delighted to see our trucks already outperforming those simulations.
“We are seeing battery efficiency (and range) impacted by the different weights the vehicles carry, the different areas the vehicles are operating in and, of course, driver training is going to be critical.”
Obsessive fuel efficiency measures aren’t new to the industry, but in the current public eHGV charging environment, an efficient eHGV driver could also be the difference between the truck making it back to the depot or not.
The data story starts now
Now the first eHGVs have been delivered under the Electric Freightway programme, and with many more to come, the hard work can start. Principal partner Hitachi ZeroCarbon will begin gathering data from the new vehicles, the charging infrastructure used, the drivers and fleet managers involved, to gain both the quantitative and qualitative insights necessary to support a successful decarbonisation pathway. And the fact that A.F. Blakemore & Son is a first mover will prove advantageous in the coming years.
“The data we’re collating across all the different routes is going to help provide that bigger holistic picture necessary to understanding how those vehicles perform,” explains James Comer, Programme Director at Hitachi ZeroCarbon. The fact we can gather more information over a greater period, compared to both competitors and peers in the industry, will help the future route-mapping and business modelling for this company.”
We’ll be revisiting A.F. Blakemore & Son to see how they get on with their electric trucks and GRIDSERVE-supplied High Power eHGV charging depot, and we’re looking forward to seeing many other hauliers follow their lead in the coming months.
Main picture from left to right: James Comer (Hitachi ZeroCarbon), Sam Clarke (GRIDSERVE), Andy Wilmot (A.F. Blakemore & Son), James Evitts (A.F. Blakemore & Son), Alistair Barnes (Innovate UK) and Dave Higgs (A.F. Blakemore & Son)
Like this?
Read the full press release
Learn more about the Electric Freightway